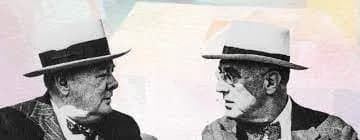
From Ancestral Art to the World's Runways
Panama Hat: Handwoven Luxury,
An icon of luxury and tradition, handwoven in Ecuador and admired worldwide.
Bravo Hats History
History of the Panama Hat
An Ecuadorian artisanal legacy
The toquilla straw hat, globally known as the "Panama Hat," represents one of the most refined expressions of Ecuadorian craftsmanship. Its history intertwines with Ecuador's cultural identity and bears witness to centuries of tradition, skill, and dedication.
Despite its name, these extraordinary hats originate from Ecuador, where communities of artisans have perfected the art of toquilla straw weaving, creating pieces that are cherished worldwide for their exceptional quality.
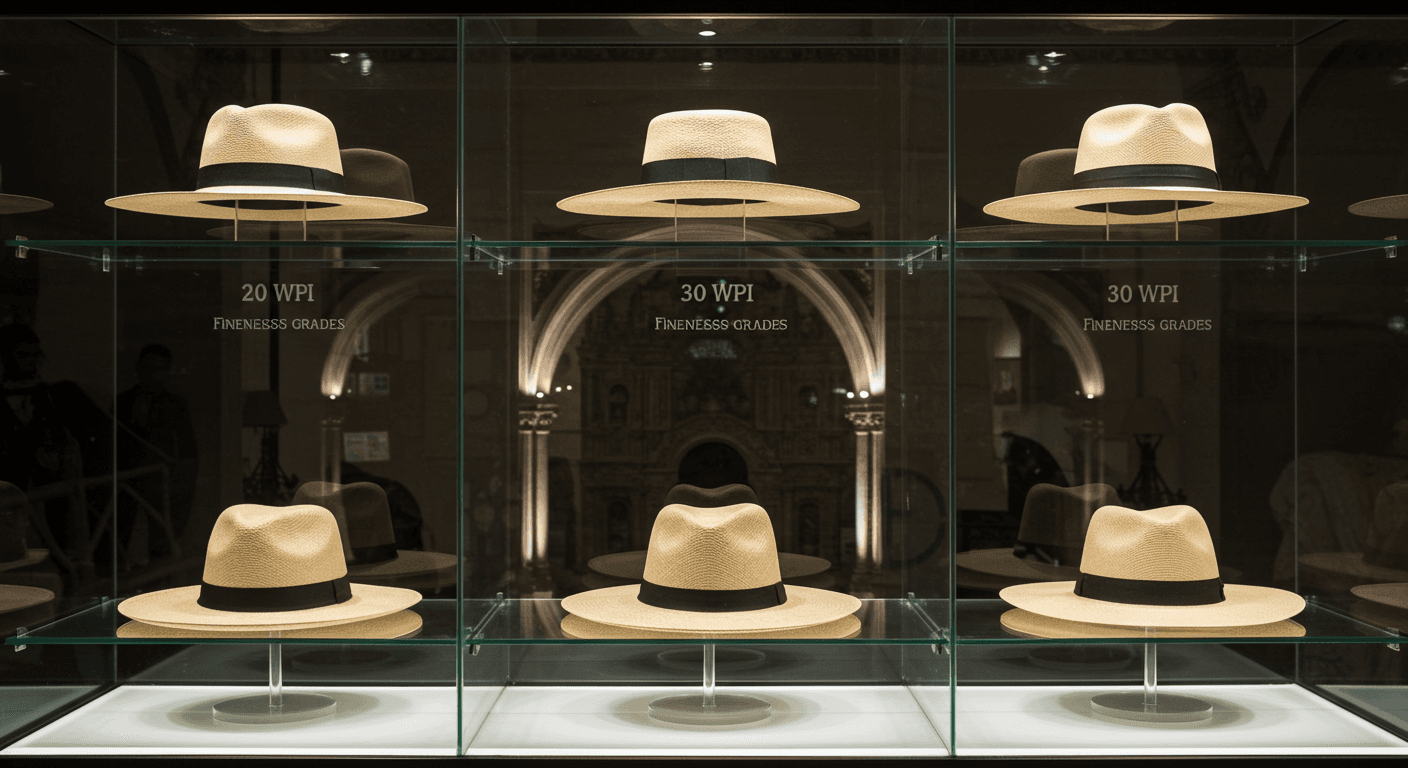
Ancestral art
Weaving a superfine hat can take up to 6 months of meticulous work, primarily done in the early morning hours when humidity is ideal.
Historical timeline
A journey through the most significant moments in the history of the Panama Hat, from its ancestral origins to its recognition as Intangible Cultural Heritage.
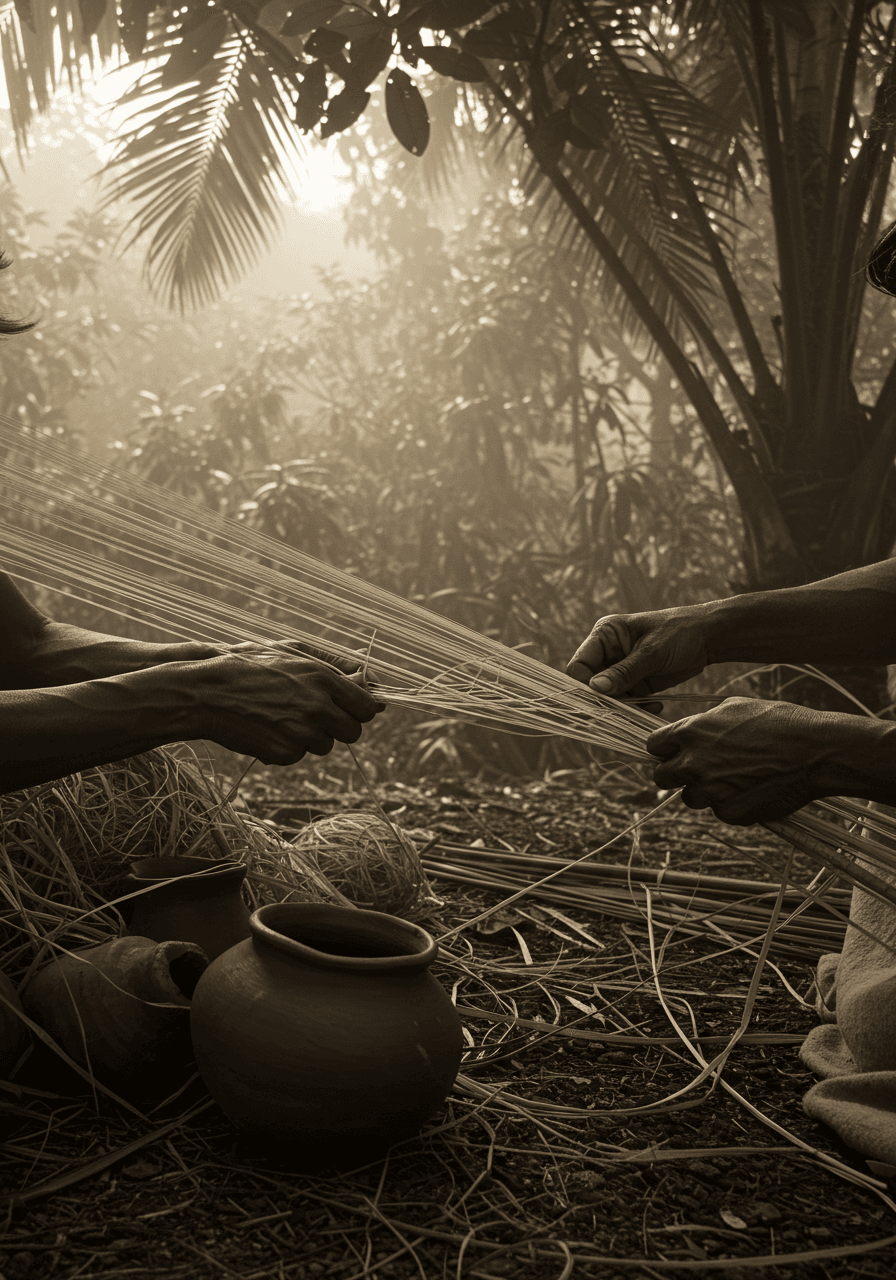
Origins
Indigenous peoples of the Ecuadorian coast begin weaving hats using the toquilla palm fiber (Carludovica palmata), developing techniques that would be passed down through generations.
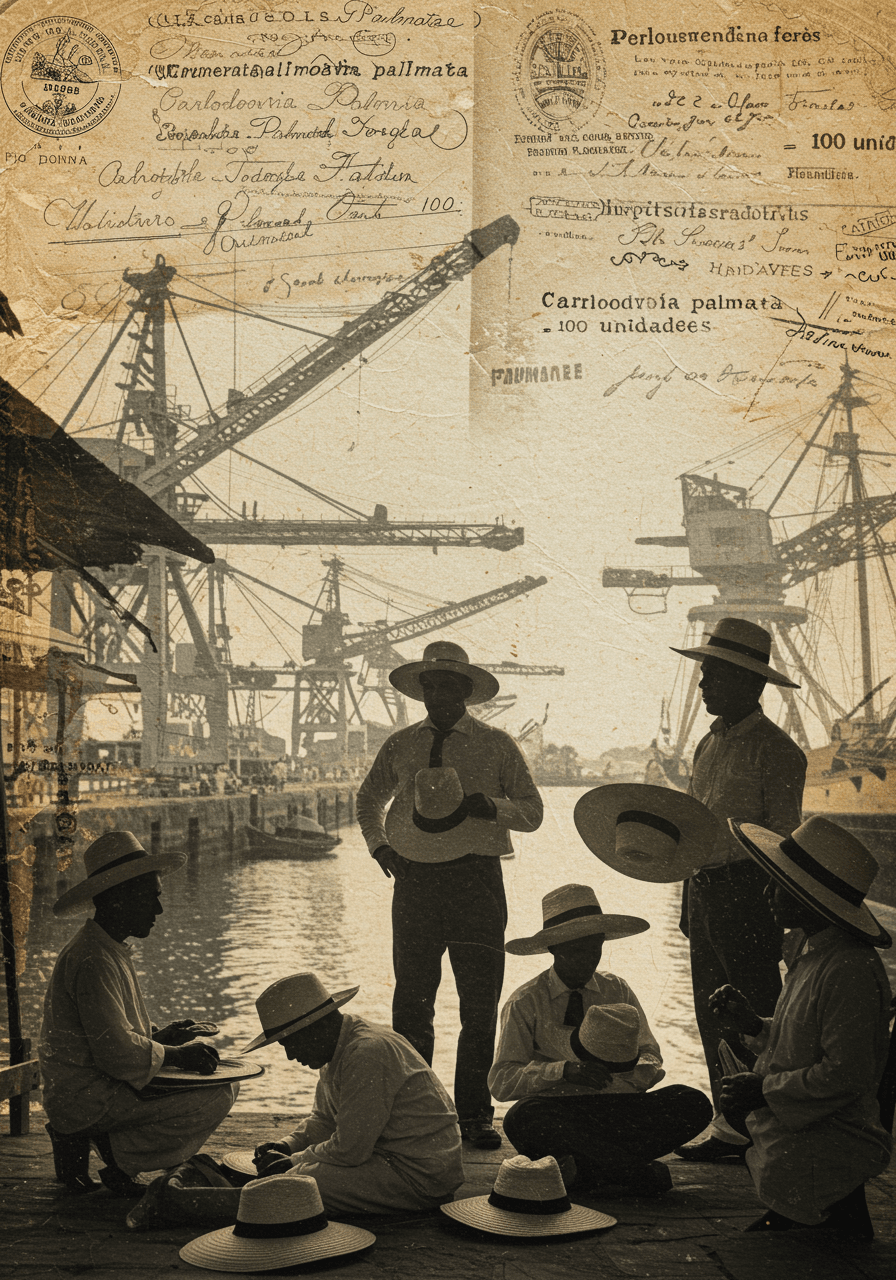
First exports
International trade of toquilla straw hats begins to flourish, with the first significant exports from Ecuador to Panama, which served as a distribution point.
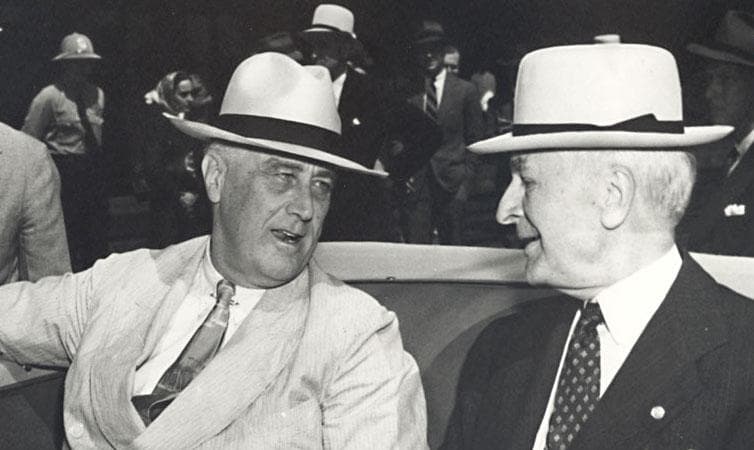
Paris World Exhibition
Ecuadorian hats are presented at the Paris World Exhibition, where they capture international attention for their extraordinary quality and weaving technique.
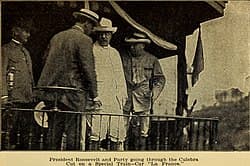
The Panama Canal
During the construction of the Panama Canal, President Theodore Roosevelt is photographed wearing the hat, popularizing it as the 'Panama Hat' despite its Ecuadorian origin.
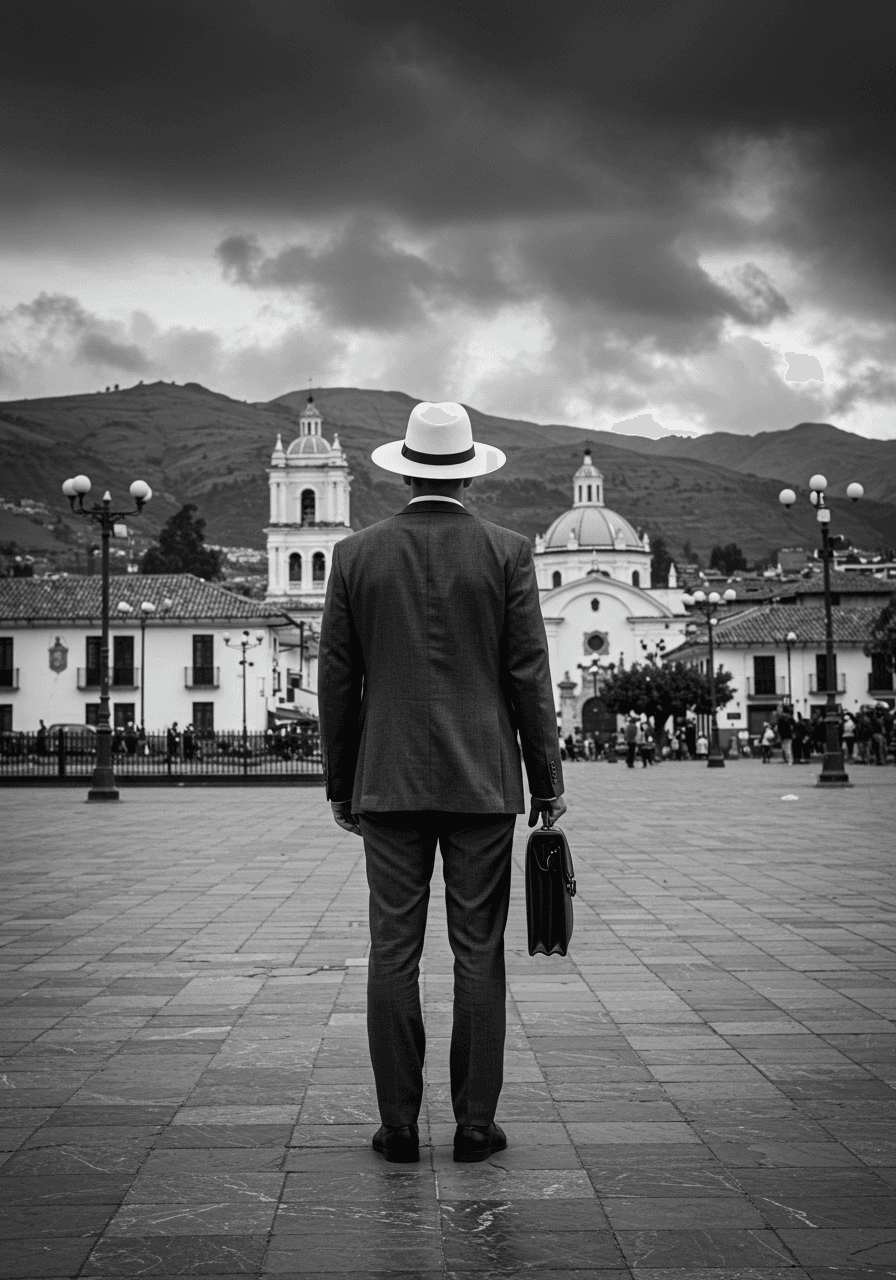
Worldwide recognition
The Panama Hat becomes a symbol of elegance and distinction, worn by Hollywood celebrities and public figures worldwide, establishing itself as a timeless luxury accessory.
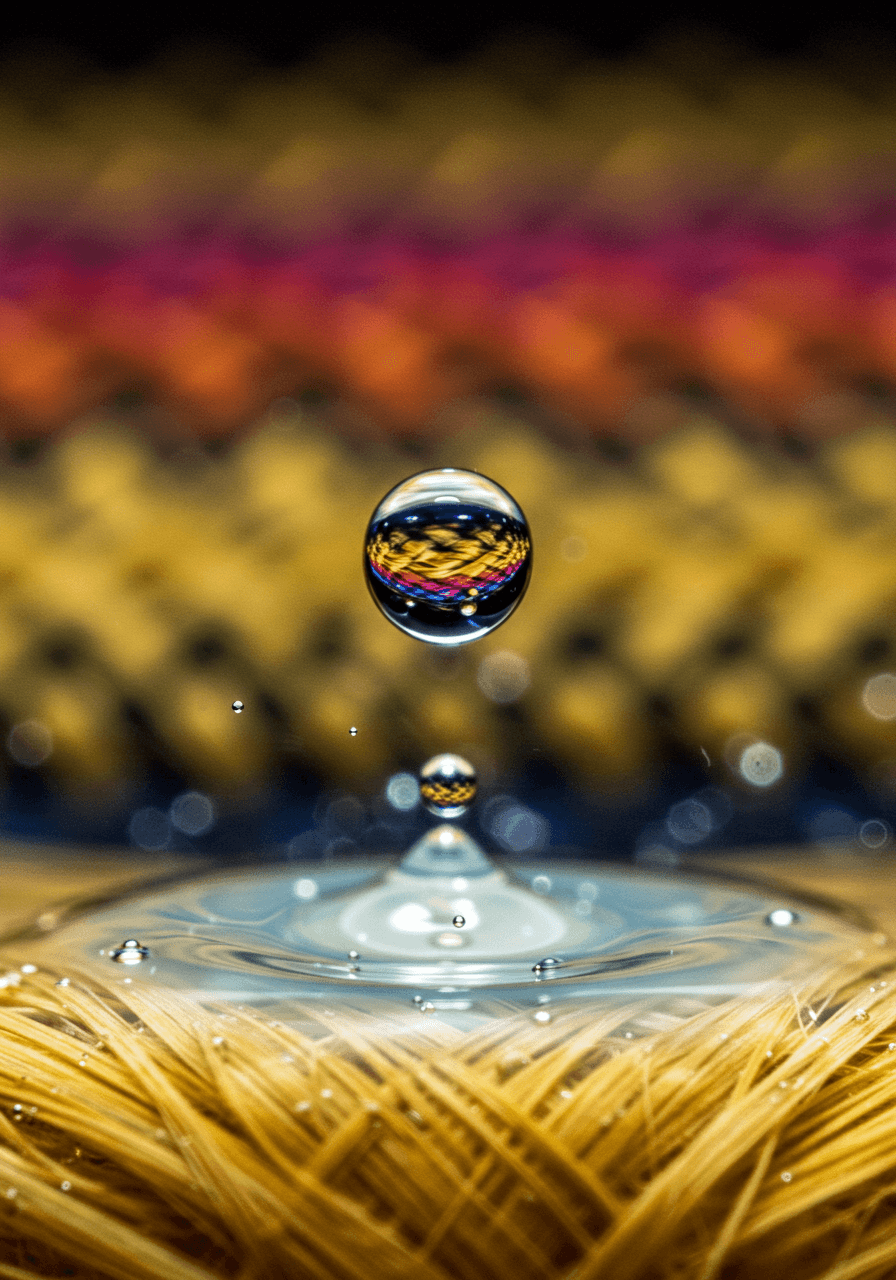
Cultural Heritage
UNESCO declares the traditional weaving of the Ecuadorian toquilla straw hat as Intangible Cultural Heritage of Humanity, recognizing its historical and cultural importance.
Distinctive characteristics
Hand weaving
Each hat is handwoven by specialized artisans, without using machinery in the fundamental weaving process.
Weave fineness
Quality is determined by the number of turns or 'weaves' per inch. The higher the number, the finer and more valuable the hat.
Flexibility
A true high-quality Panama Hat can be rolled without damage, a characteristic known as 'rollable hat'.
Lightness
Despite their durability, the hats are extraordinarily light, providing comfort in warm climates.
"True elegance is recognizing the quality of what not everyone can see."
Manufacturing process
Straw harvesting
Selection and collection of young stems of Carludovica palmata, known as toquilla straw.
Fiber processing
Cooking, drying, and bleaching of the straw to obtain the appropriate flexibility and color.
Strand separation
Manual division of fibers into fine threads, determining the final quality of the hat.
Crown weaving
Starting the hat from the top center, establishing the weaving pattern.
Body and brim weaving
Continuing the spiral weaving outward, forming the body and brim of the hat.
Finishing and completion
Finalizing the edges, blocking the shape, and applying final finishes.
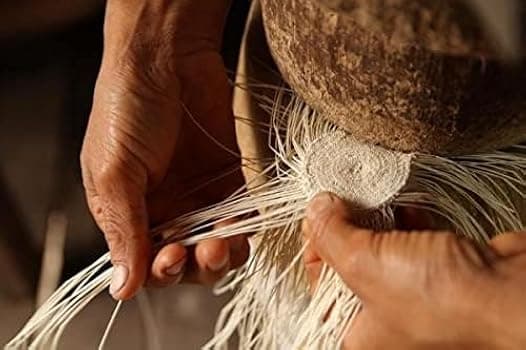
The hat weaving is traditionally done in the early morning hours or at dusk, when the air humidity allows the fiber to maintain its ideal flexibility.
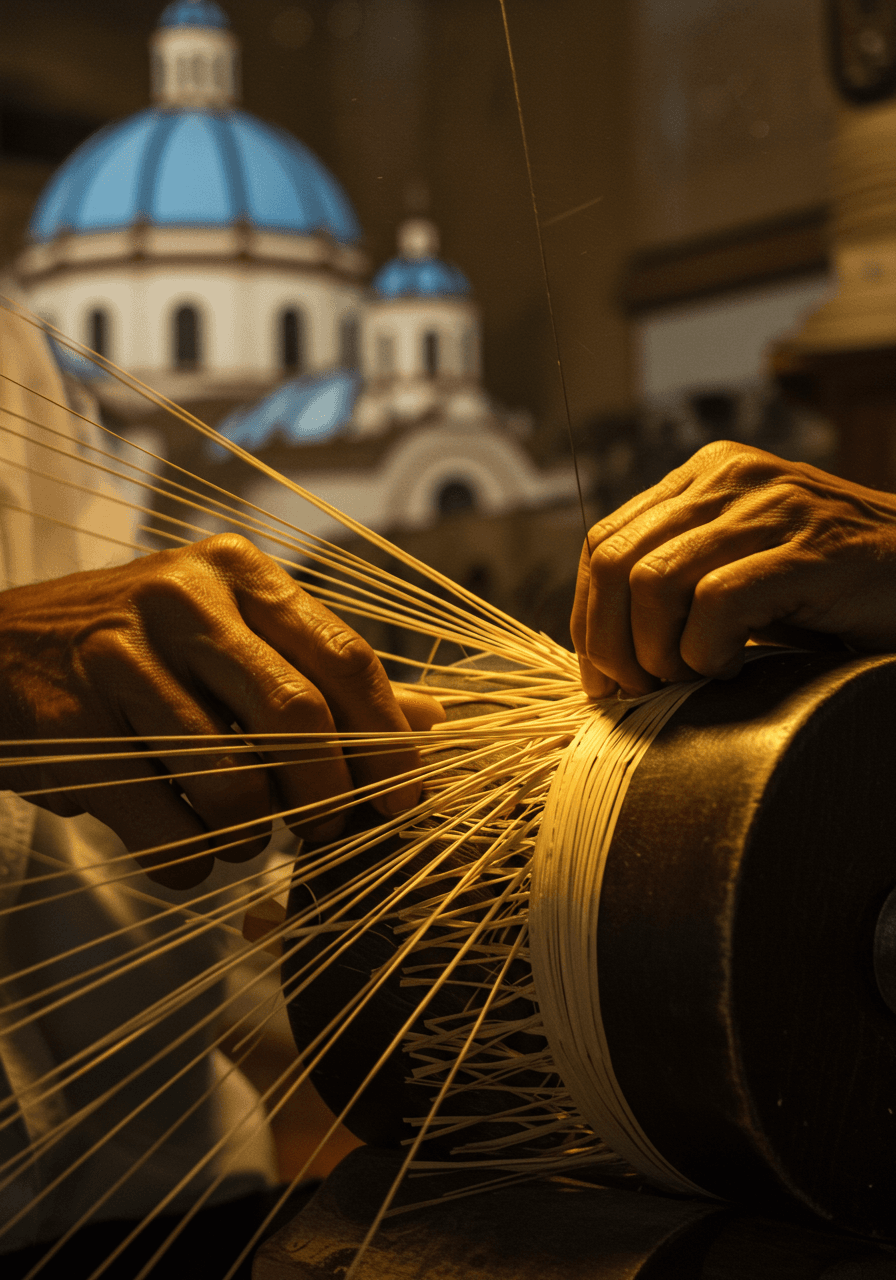
Behind every Panama Hat lies a story of patience, mastery, and deep respect for tradition. It is more than a hat; it is a living testament to our cultural heritage.
Safeguarding Committee
Traditional toquilla straw hat weaving
Currently, the main production areas of the authentic Panama Hat are located in the Ecuadorian provinces of Manabí (Montecristi) and Azuay (Cuenca), where thousands of artisans keep this centuries-old tradition alive.
Authenticity
How to recognize an authentic Panama Hat
The true Panama Hat, woven with Ecuadorian toquilla straw, is an artisanal masterpiece recognized as Intangible Cultural Heritage of Humanity by UNESCO. Distinguishing an authentic specimen requires attention to specific details.
Ecuadorian Craftsmanship
Each hat is a unique masterpiece, handwoven by expert artisans.
Uniform Weave
An authentic Panama Hat features a meticulously uniform weave, with no visible irregularities in its structure.
Flexibility
Original hats can be rolled without damage and return to their original shape, demonstrating the quality of the fiber.
Lightness
Genuine toquilla straw is extremely lightweight; a high-quality hat is barely noticeable when worn.
Interior Seal
Authentic Panama Hats bear a seal of origin and, in many cases, the signature of the weaving artisan.
Expert Advice
Please note that some merchants sell hats under the name 'Panama Hat', but the truth is that most of these hats are manufactured in Colombia, Peru, or China, where the material used to make hats are other types of low-quality weaves such as Iraca, Tetera, and Enea. These materials have much lower quality and durability than our Ecuadorian toquilla straw.
"The true Panama Hat is only woven with Ecuadorian toquilla straw"
Panama Hat Lexicon
Vocabulary and key terms of our craftsmanship
The world of authentic Panama Hats has its own vocabulary, born from centuries of Ecuadorian artisanal tradition. Discover the terms that define this manifestation of intangible cultural heritage of humanity.
Toquilla Straw
Ecuadorian coast
Natural fiber obtained from the Carludovica palmata palm, native to Ecuador. Its flexible texture and resistance allow for the characteristic fine weaving of the hat.
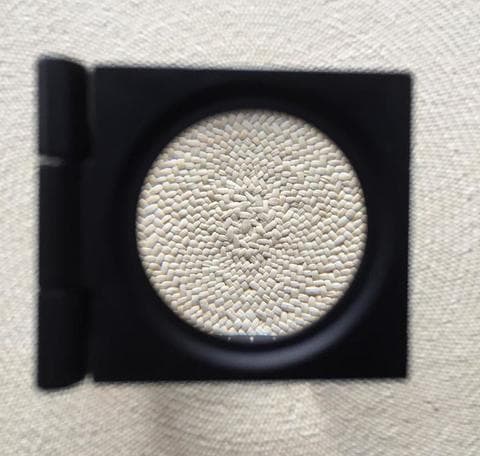
Weave Grade
International standard
Classification system indicating the fineness and quality of the hat. Ranges from grade 1 (coarser) to grade 20 or higher (extremely fine). Higher grades can take up to 8 months to weave.
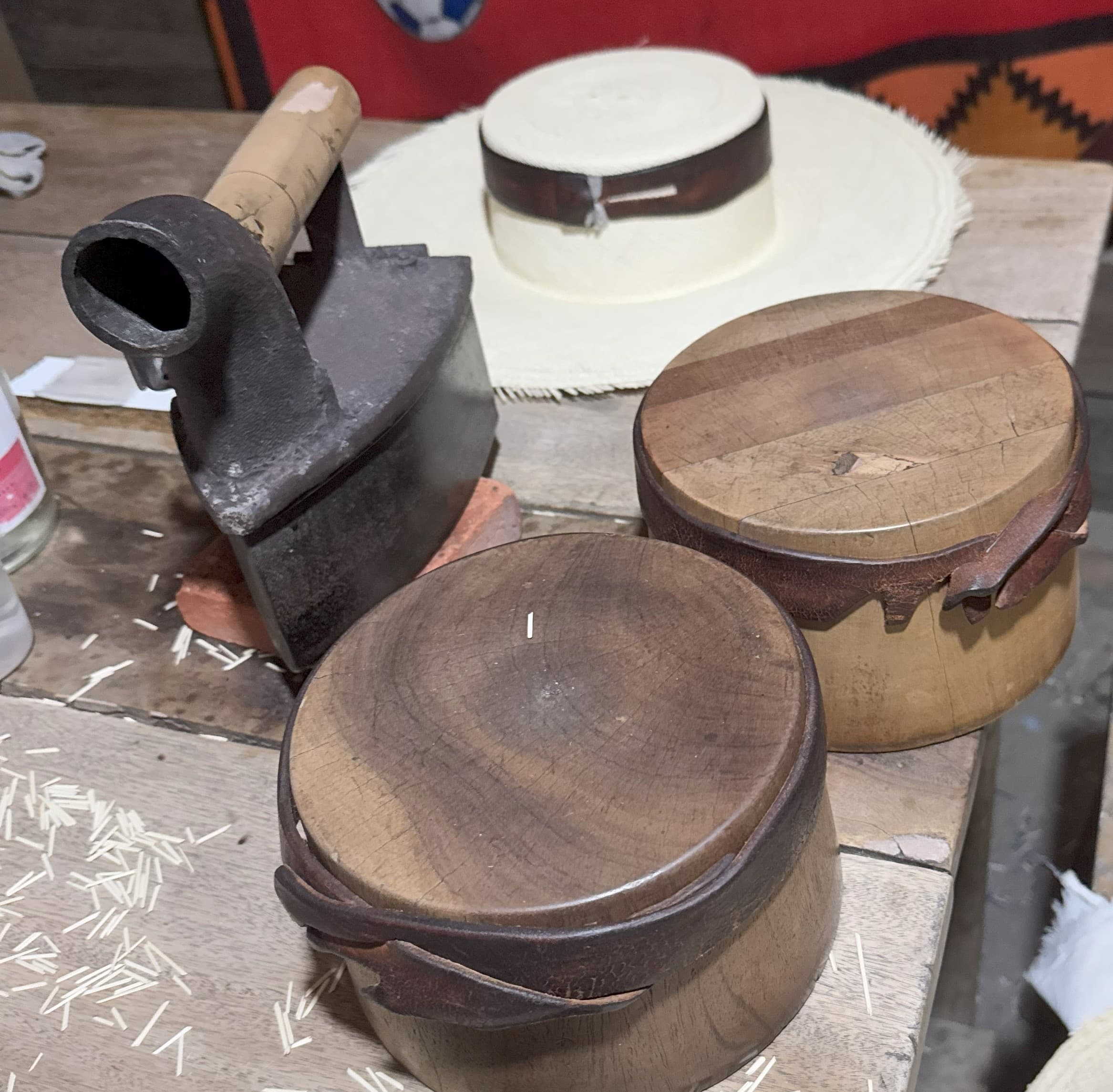
Pressing
Ecuador
Final process of smoothing the hat with heat and pressure to ensure a neat and uniform finish.
Blocking | Pressing
Cuenca and Montecristi
Process of shaping the hat using wooden molds (blocks) and applying pressure and steam. Defines the style and final silhouette of the hat.
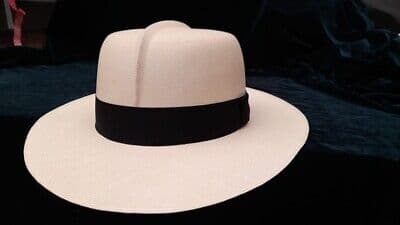
Montecristi Fine
Montecristi, Manabí
Premium classification designating the highest quality hats woven in Montecristi, Ecuador. Characterized by its extraordinarily fine and uniform weave.
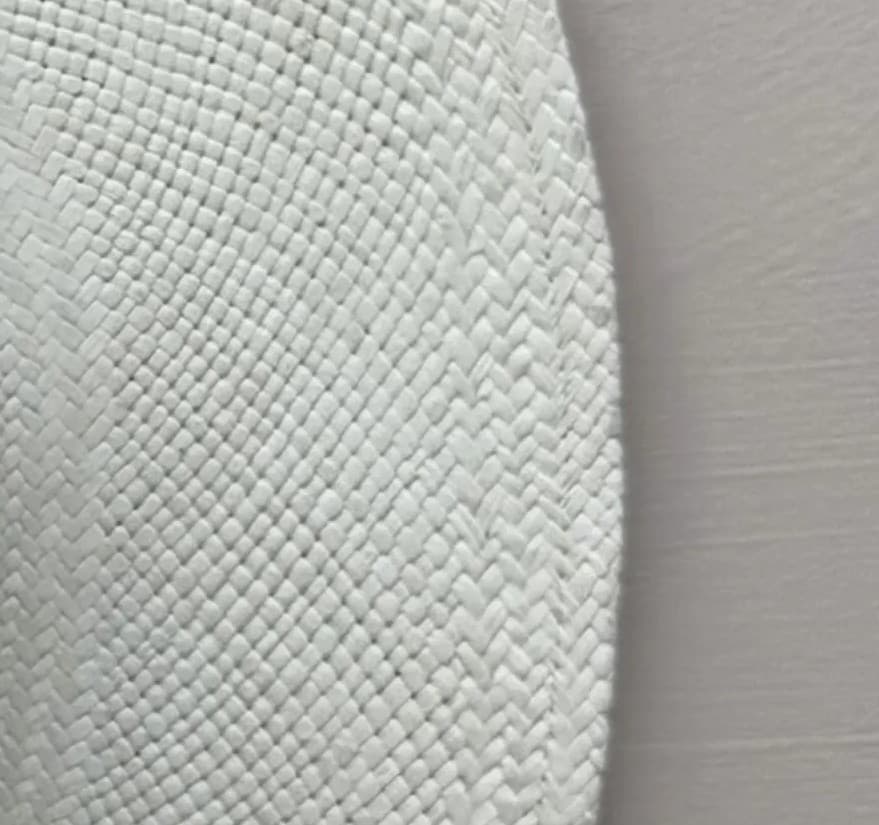
Edge Finishing
Universal technique
Technique for finishing the hat's brim, where fibers are folded and interwoven to create a clean and durable finish.
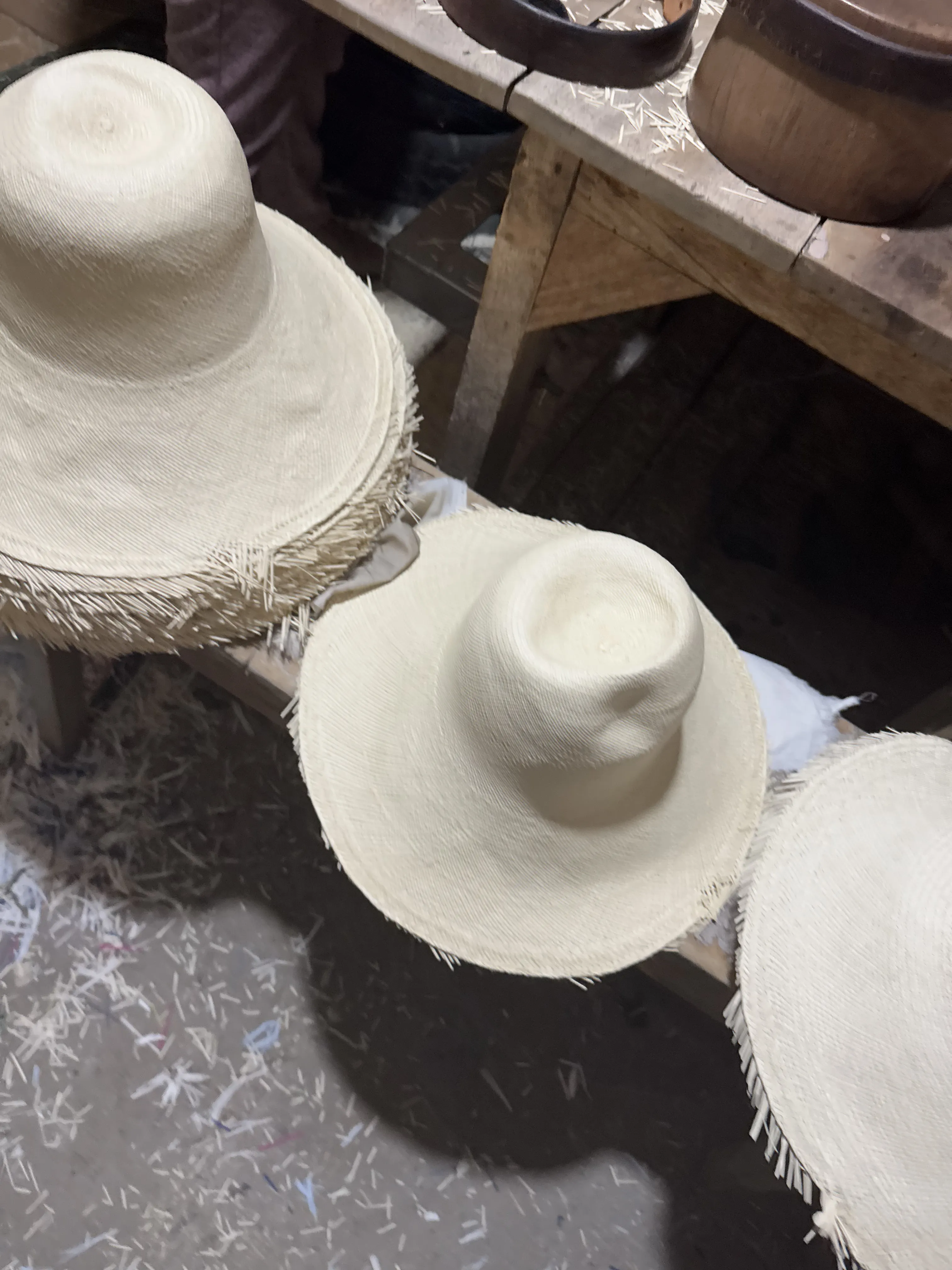
Tightening
Traditional Ecuadorian technique
Process of adjusting and tightening the woven fibers to ensure uniformity and strength of the hat's structure.
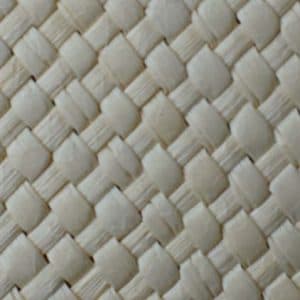
Brisa Weave
Cuenca, Ecuador
Weaving pattern with small, regular holes, offering greater ventilation and freshness.
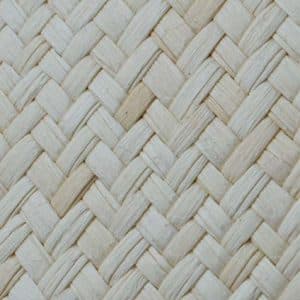
Plain Weave
Ecuador
Compact and uniform weaving style, without visible perforations.
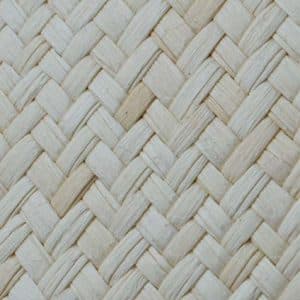
Cuenca Weave
Cuenca, Ecuador
Characteristic weaving style of hats produced in Cuenca, Ecuador. Distinguished by its more pronounced and visible weaving pattern compared to plain weave, giving it a unique appearance.
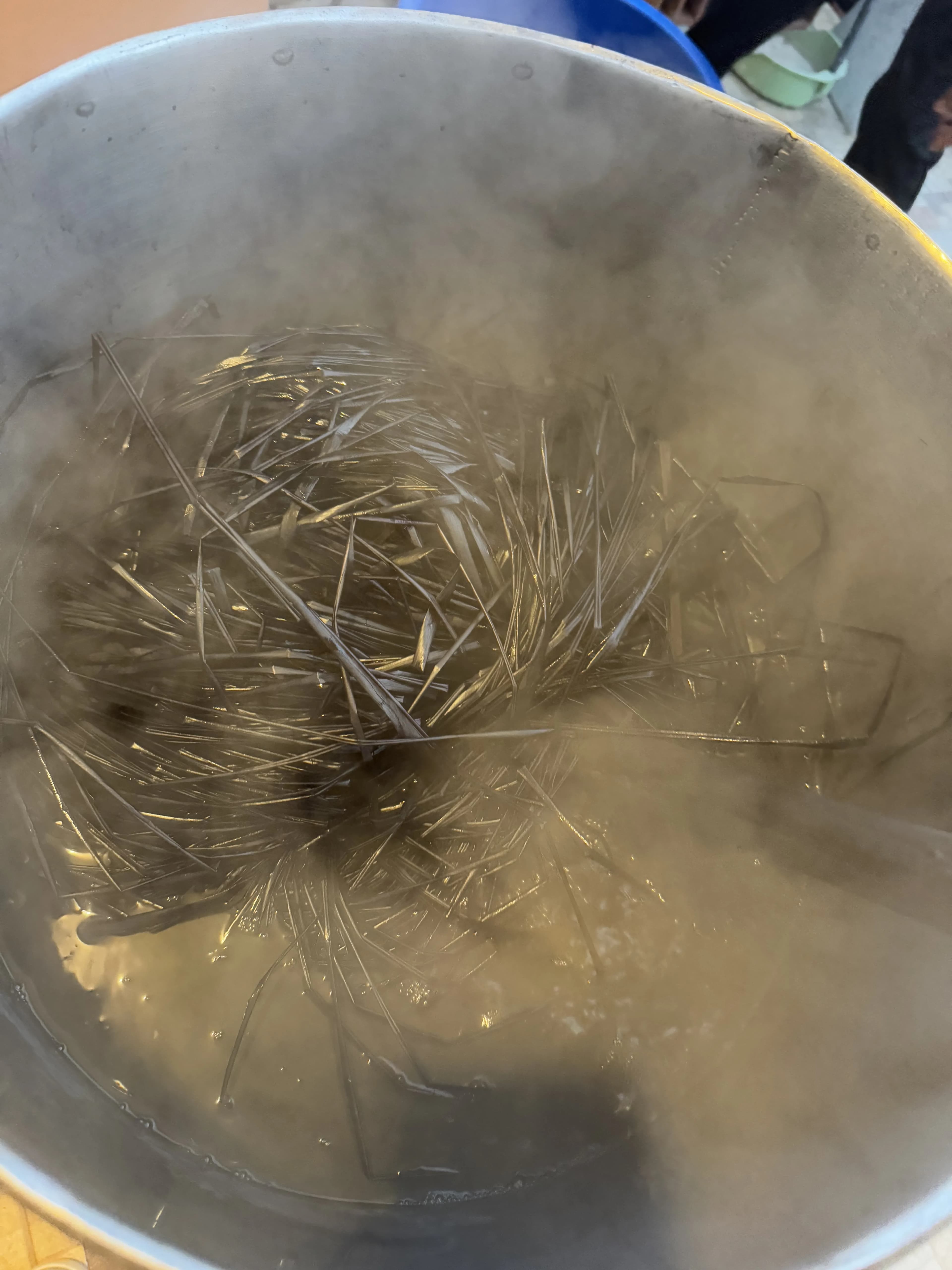
Dyeing
Ecuador
Process of coloring toquilla straw using natural or synthetic dyes to obtain hats of different colors.
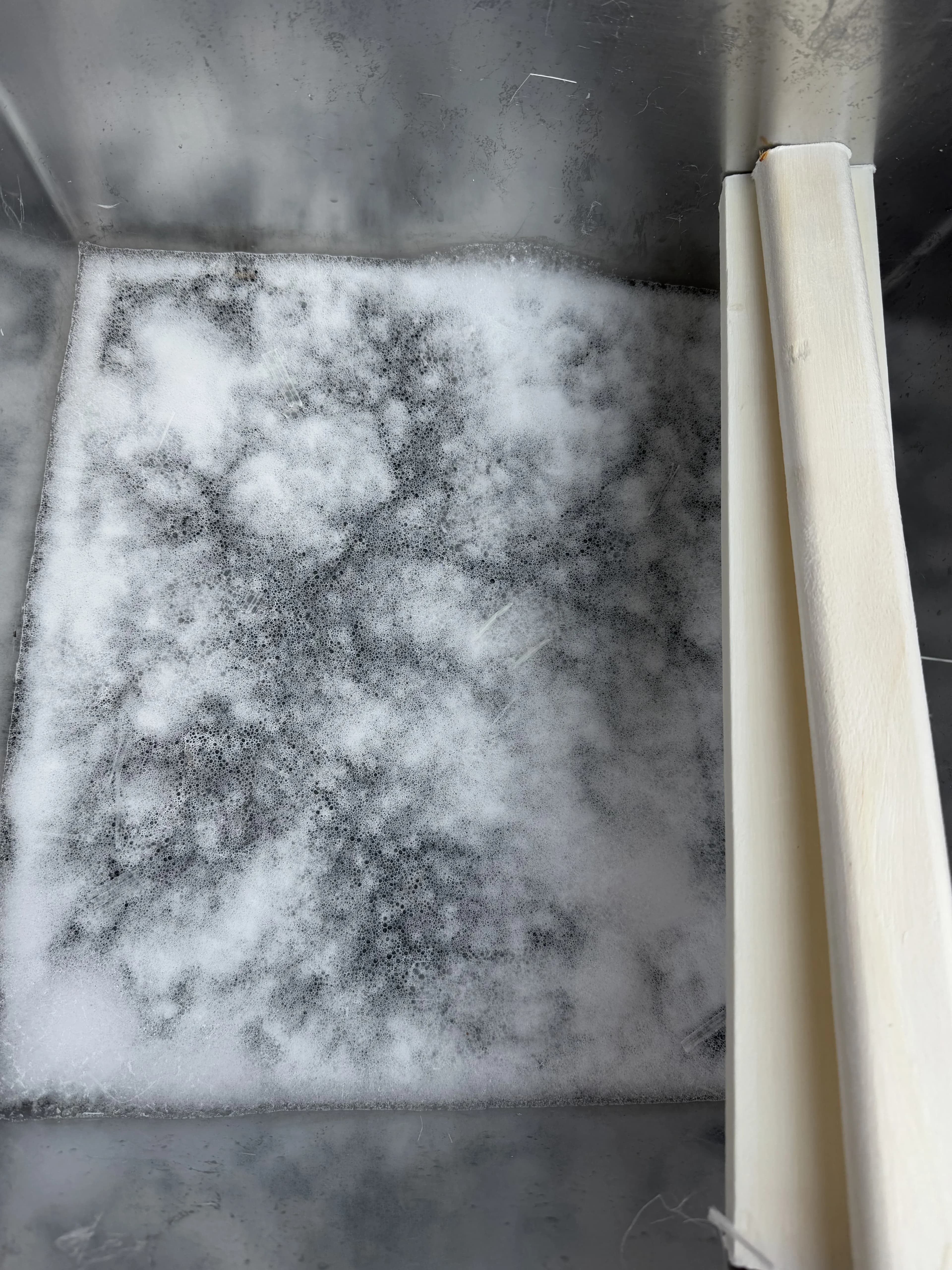
Bleaching
Ecuador
Treatment with natural or chemical products to lighten the color of toquilla straw and achieve white or ivory tones.
Cultural Heritage
The traditional weaving of the Ecuadorian toquilla straw hat was declared Intangible Cultural Heritage of Humanity by UNESCO in 2012, recognizing centuries of artisanal tradition passed down from generation to generation.
Despite its name "Panama Hat," these hats are 100% Ecuadorian. The name comes from their international popularity during the construction of the Panama Canal, where they were used by workers and later marketed from that country.